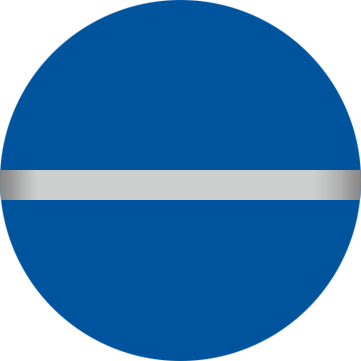
Continuous Innovation is Chi Chang's Promise to Customers - Verticalizing Stretching Units Saves 20% Space and Labor Costs
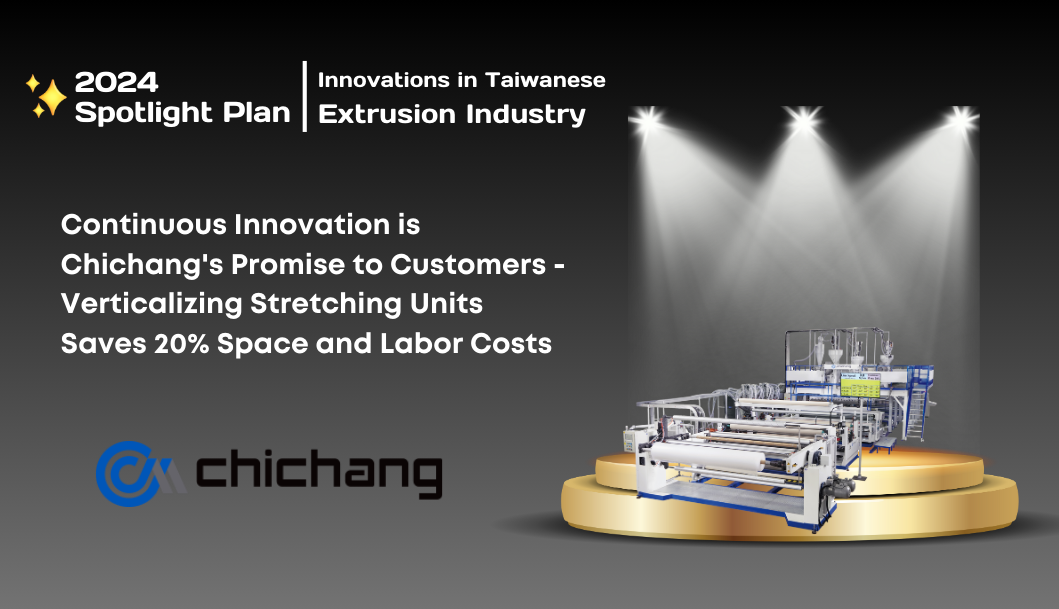
The extruder is the type of plastic and rubber machinery that values customization the most. It's not just about catering to customer needs through changes, but also proactively seeking innovations in line with changing times. This allows the machinery to perform at its highest efficiency, helping customers achieve optimized production while striving to reduce costs for maximum profitability.
Valuing customer feedback: A glimpse of innovation from on-site workers
Chi Chang excels in the design and manufacture of plastic extrusion machinery, especially since most extruders are customized. Regulations vary between countries, and production environments differ, coupled with the ever-changing material formulations. Each machine undergoes extensive communication to confirm machinery details, production processes, material characteristics, and final product specifications to design and manufacture a machine that meets customer needs.
"Each machine involves significant investments ranging from hundreds of thousands to millions of dollars. Such large-scale investments entail enormous losses to both sides if anything goes wrong. Therefore, thorough confirmation is essential before signing any contracts. Many customers are amazed by our willingness to patiently communicate," explained Johnny, Chairman of Chi Chang. "I often find myself communicating with customers until three or four in the morning, or even flying to the United States or Italy just to explain the details in person. What touched me the most is that many of our customers are willing to allow me to bring potential clients to their factories to see the machines"
This level of openness is rare. After all, allowing Chi Chang to bring other clients to visit machine operations in their active factories requires immense trust and signifies deep cooperation with the clients.
Why do customers trust Chi Chang so much?
"Our job doesn't end with the delivery of the machine. After inspection and delivery, we continue to monitor our customers' production conditions, understand any problems encountered by their on-site workers, and ensure smooth machine operation," shared Tom, Chi Chang's General Manager. Prioritizing customer experience and service communication is not limited to decision-makers or managers; often, feedback from on-site workers is the most genuine and challenging.
"However, sometimes, workers' complaints become opportunities for innovation and change," Tom said with a smile while his eyes gleaming. The issues raised by workers are frequently the key to advancing the line.
Striving for Better: Erecting the flat stretching unit!
Chi Chang's extruders encompass a broad spectrum of products, ranging from bubble film, breathable film, foam extrusion, sheet extrusion, hollow profile sheet extrusion to recycling systems. Each piece of equipment is crafted with precision, with ongoing enhancements driven by feedback from operators to optimize performance and cost-effectiveness.
Recently, the upcoming shipment of the PE Breathable Film Extrusion Line to India is a classic example.
The quality of the breathable film primarily depends on the smoothness and uniformity of its thickness. Maintaining minimal thickness deviation is crucial, especially at a production speed of 250 meters per minute, where the film traction needs to be stable. Besides ensuring the extruder's efficiency and stability, the proper control of the traction and stretching unit extension is essential.
Traditionally, stretching units were designed flat. However, based on feedback from customers, Chi Chang identified inconvenience during maintenance due to the low position of the maintenance area, making parts replacement challenging. Therefore, Chi Chang decided to erect the stretching unit!
By erecting the stretching unit, the machine's required floor space is reduced by at least 20%. Additionally, the previously ground-level position is now easily accessible, facilitating problem detection through a working platform, making disassembly, maintenance, and cleaning easier. With the machinery being less "lengthy" than before, only two workers are needed for high production output 24 hours a day. This not only significantly reduces the factory's space requirements but also lowers labor costs, addressing the current labor shortage issue.
Exceptional machinery quality goes beyond investment—it's about applying this tactic.
Aside from the innovative breakthroughs in machines, Chi Chang also shares their secret to maintaining a certain level of machinery quality: "It's all about using the best!" Tom generously remarked.
In fact, the high cost of extrusion machines is due to many critical components being sourced from world-renowned manufacturers. Take, for instance, the core component of the PE Breathable Film Extrusion Line, the die head, which comes equipped with state-of-the-art thickness inspection and automatic correction devices. The thickness inspection device in the traction section continuously feeds back thickness data to the die head. Once a deviation occurs, the die head automatically adjusts the amount of material extruded, reducing thickness deviation and significantly increasing film yield.
"Many clients demand exceptionally high standards, and we've experimented with various molds. Now, armed with a wealth of data, we tailor the selection of components from reputable brands to meet the specific standards required by clients," Tom candidly stated. When asked whether competitors using similar top-tier components could achieve machinery of the same caliber as Chi Chang's, Johnny chuckled and said, "Not that easy."
He also inquired why clients choose Chi Chang. Their responses touched him deeply and brought him comfort. "Our clients in Australia said they not only consulted with us but also with several well-known manufacturers. However, only Chi Chang responded promptly to their inquiries and provided the most comprehensive information. Our proactive attitude left a lasting impression on them. Most importantly, we demonstrate to clients that purchasing from Chi Chang yields visible results."
Through Chi Chang's sharing, it's evident that the most crucial element for successful innovation is customer 'confidence.' To gain customer confidence, timely responses, comprehensive and understandable information, patient and proactive cooperation are essential, culminating in clients witnessing the anticipated results.